Back to the main page of ENGIE's vigilance plan
The ENGIE health & safety vigilance approach
For ENGIE, health & safety is a top priority. Protecting the lives of all those who work for the Group is at the heart of what we do as a socially responsible company.
The Group's prevention actions are structured in 3 areas:
- "No life at risk", mitigation of risks related to the direct performance of activities, prevention of accidents at work;
- "No mind at risk", improvement of the well-being at work, vigilance, control of psychosocial risks related to the context of execution of activities;
- "No asset at risk", mitigation of the risks related to the Group's industrial activities.
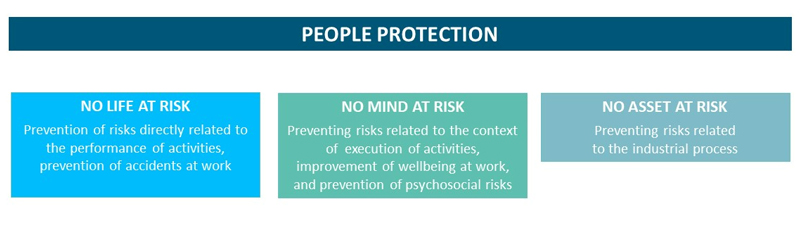
A. Risk Mapping
The mapping of occupational health & safety and process safety risks is established as close as possible to the field by each entity, according to its activities and geographical locations. These risks are indeed very marked by the businesses and environments in which they are carried out, and specific to each entity.
They are the subject of periodic reviews in order to take into account all the evolutions of the businesses and the feedback of experience following the near miss accidents and accidents that have occurred.
The most serious occupational accidents occurring within the Group are related to work at height, electrical risk, lifting activities and road risks. These risks are the subject of specific prevention rules and specific training and awareness-raising (authorizations, guidelines, communication actions, etc.).
In addition, the Group identifies, analyzes and mitigates events with high potential of severity (HiPo), events that are precursors to serious accidents. HiPo analysis confirms the identification of the most critical risks mentioned above.
B. Assessment of subsidiaries
The Group's health & safety rules apply to all entities for which ENGIE holds operational management, regardless of their mode of financial consolidation, in addition to the business rules issued by the subsidiaries. Various measures are put in place to assess compliance with these rules by the Group's employees and subcontractors, as well as the mitigation of health & safety risks. Safety visits are performed by managers, audits and inspections make it possible to assess the compliance of practices with the standards in force, risk reviews are held periodically, evaluations by internal control are completed each year.
In addition, the Group's entities are subject to internal audits by the Group Audit Department. These audits systematically include compliance with ENGIE's health & safety measures.
The Group's entities also conduct their own audit programs in addition, depending on the health & safety risks identified, or as part of a certification process for the entity's occupational health & safety management system (e.g. ISO 45001 or OHSAS 18001 certification, MASE certification in France or VCA in Belgium).
The process safety of the facilities on which the Group operates is the subject of sustained attention through the implementation by subsidiaries of dedicated management systems and specific investments. Audits of the installations concerned are carried out regularly. Thus, ENGIE's Insurance Department defines an annual audit program for the Group's industrial assets, which is entrusted to a specialized external service provider. These audits specifically target risks of fire, machinery breakdown and natural disaster. The objective is to visit the Group's most important industrial assets at least once every 3 years.
External audits can also be carried out by local public authorities, depending on the applicable regulations (e.g. periodic audits of so-called Seveso industrial facilities in Europe, depending on the potential risks to property, people and the environment).
C. Risk treatment actions for health & safety
a) Group commitments
ENGIE has implemented a policy of excellence to ensure the best possible working conditions for the Group's employees and subcontractors around the world. To this end, the Group has set a health & safety policy, signed European and global agreements with employee representatives, and defined a framework and rules to make everyone, leader, manager or employee, a committed player in their health & safety.
The Group has set itself ambitious objectives that have the particularity of concerning anyone working for the Group, employees as well as subcontractors. They testify to our determination to do everything possible to eradicate accidents at work, especially the most serious of them.
ENGIE's health & safety policy details the Group's 8 fundamental principles in terms of health & safety:
- Taking risks into account in any decision-making process
- Participatory approach to the prevention of risk situations
- Promotion of a climate of trust and exchange
- Prioritization of prevention
- Benchmarking, sharing and feedback
- Level of prevention and protection for our subcontractors at least equivalent to that of our employees
- Compliance with regulations and internal rules
- Preparing for crisis management
These commitments made by ENGIE for many years at European level as part of the Group Agreement on the Fundamental Principles on health & safety of 2010, were reinforced and extended in 2014 to the entire Group, by the Global Agreement on health & safety at work concluded with employee representatives. The Global Social Agreement signed in 2022 was an opportunity to update the Group health & safety agreement signed in 2014.
b) Risk treatment actions
The Group's health & safety principles and commitments are implemented through specific action plans defined at the Group's various levels of organization.
The main actions implemented by the Group in 2021 are presented in the extract from the Universal Registration Document available below.
c) Prevention of serious and fatal accidents
In accordance with the Group's health & safety policy, the prevention of serious and fatal accidents is based on a hierarchy of risk prevention aimed at implementing, in order of priority:
- measures to eliminate risks at the source
- collective organizational and protection measures
- personal protective measures.
The specific prevention measures deployed by the Group to combat serious and fatal accidents are:
- The nine Life Saving Rules, to be respected in all circumstances and by all.
- Systematic identification, analysis and treatment of events with high potential of severity ("HiPo"), precursors to serious accidents.
- Instruction given to employees and subcontractors to stop activities if all safety conditions are not met ("Stop the work" approach).
- The last-minute risk analysis ("the minute that saves"), which consists of carrying out before any intervention a new and final risk assessment in the field to ensure that the risks are under control.
- Finally, the Group also expects its employees to be attentive to the safety of all other people, regardless of their status: colleagues, temporary workers, subcontractors, etc. (so-called "shared vigilance" system).
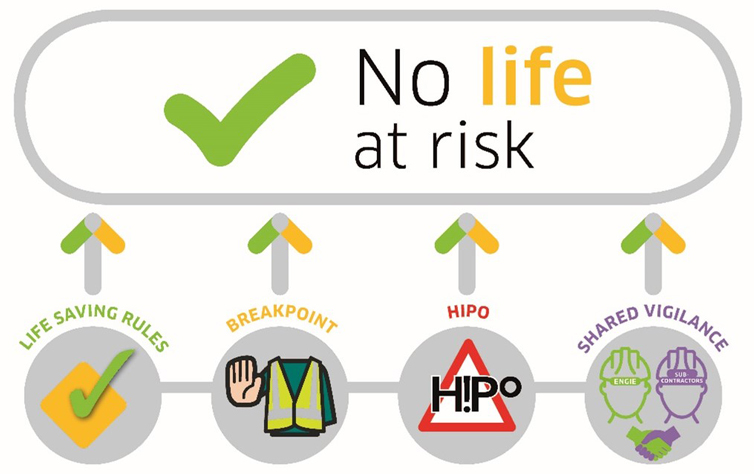
>> Consult ENGIE's brochure Preventing serious and fatal accidents <<
D. Monitoring of results
The monitoring of health & safety results allows the Group and its entities to evaluate the efficiency of the risk treatment measures implemented.
Health & safety results are monitored operationally through:
- a health & safety reporting system integrating reactive indicators (focused on the occurrence of accidents) and proactive indicators (to monitor the situation of entities before accidents occur).
- an internal control process, with several frameworks devoted to occupational health & safety and process safety. The various health & safety risks are covered by frameworks devoted to industrial projects (IND1), operational industrial processes (operation & maintenance, IND2-IND3), safety of industrial control systems (IND4), crisis management and communication (COR5) and occupational health & safety (COR8a).
- certification by the statutory auditors, prior to their annual publication in the Universal Registration Document.
- presentations and exchanges:
- with staff representatives at Group entities level;
- with employee representatives at Group level: health & safety topics (results, actions implemented to control risks, evolution of the Group's prevention measures, etc.) are examined by ENGIE's European Works Council and by the Global Forum set up to monitor the implementation of the Global Social Agreement signed in 2022;
- with the group's management through its Executive Committee and its Operational Committee;
- with ENGIE's directors, via the Board of Directors and its Committee for Ethics, Environment and Sustainable Development.
The results and main health & safety actions are published in detail in the annual Universal Registration Document. For any questions relating to health and safety you can contact: GroupHealhandSafetyDepartment@engie.com